July 3, 2018
With workplace injuries and accidents costing U.S. employers alone over $60 billion a year, it’s not surprising that safety has emerged as a key productivity-boosting and cost-saving application for wearable technologies and other emerging tech. I spoke with Sam Murley, EHS Digital Acceleration Leader at General Electric, about how GE is currently piloting and deploying body-worn sensors, exoskeletons, AR/VR, and more along with Sam’s vision for the future of EHS. Sam has been an inspiring thought leader at several Enterprise Wearable Technology Summits–don’t miss his case study “EHS 2.0 and The Predictive Digital Model” this October in Austin at EWTS 2018!
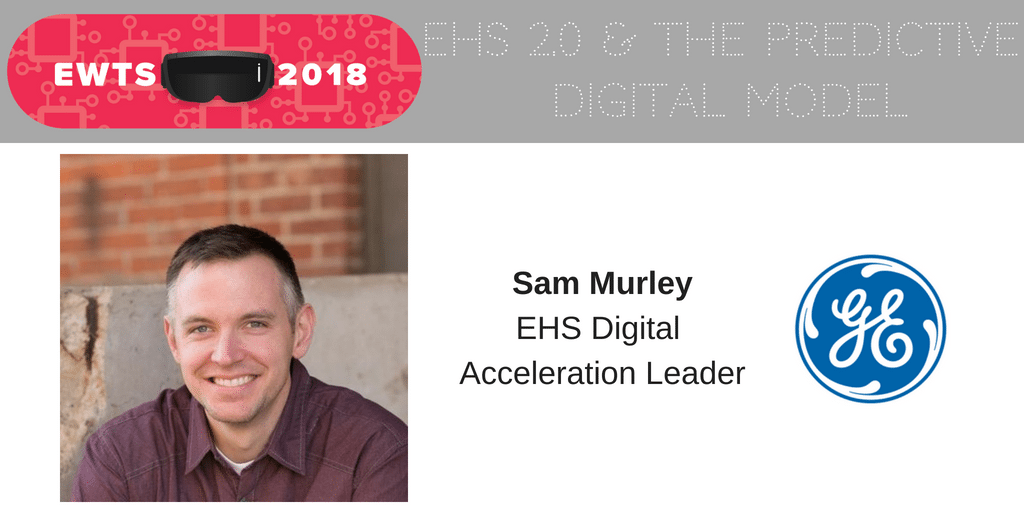
This interview has been edited and condensed for clarity.
E: To start, could you provide us with a little background on yourself and your career, and what you do at GE?
S: I’m the EHS Digital Acceleration Leader at GE and oversee the innovation and emerging technology portfolio for environment, health and safety (EHS) . Our EHS innovation portfolio focuses on incubating the exploration and accelerating the adoption of emerging technologies and wearable devices through a Pilot-to-Deployment process. The goal is to eliminate certain hazards and risks within work environments, increase safety in general, increase operational excellence, and drive efficiency to give time back to frontline EHS teams through digital means.
E: Can you give us an example of a wearable tech pilot or idea that you ran by employees and got off the ground?
S: We have roughly 2,000 wearable devices being evaluated or piloted at this time in addition to wearables that are being deployed. They fall into 6 technology categories: Smart eyewear/heads-up displays; exoskeletons and ergonomic sensors; industrial hygiene monitoring IoT devices; lone worker management devices and platforms; hazard-sensing bands; and robots and drones that can perform hazardous inspections while keeping someone safe on the ground. We have nearly 65 pilot programs running globally, supporting almost 170 individual teams.
Something really fresh and about to make it past the pilot stage are ergonomic sensors. The tech allows EHS to do what it does today but takes it from pen and paper to a sensor and connected system in order to understand who’s at most risk and why, who needs coaching or intervention—you can’t do this as effectively by watching someone over the course of a month and recording the data by hand. With wearable tech, you can do it in 24 hours.
Say John Doe was at a critical safety score nearing a back injury last week: We made changes in the work environment and his safety score went back up. Or, maybe it continued to trend down, giving EHS insights to try a form of mechanical intervention such as an exoskeleton. I think the most successful technology gives you immediate feedback while measuring some activity in the human body or environment and tying it back into a decision-making platform.
E: So, how do employees react? How do you protect employee data?
S: It is important and absolutely necessary to manage the risks that new technology can introduce. In general, for every technology we evaluate and ultimately use, we take it through a comprehensive and thorough data privacy and labor relations review. We partner with global and regional compliance teams and have a self-service innovation hub where business leaders, EHS teams, and employees can learn more about the different technologies, join a pilot, or learn how to use deployment ready wearables.
E: You mentioned robots for inspection. How can robots increase safety and productivity and for what types of use cases and tasks?
S: A few use cases come to mind such as confined space entry, where work is performed at heights, and hazardous inspections. Instead of having a worker perform a visual inspection inside a large tank, EHS can deploy tracked and aerial drones, sending the companion robot into the environment with a front-facing camera that can be controlled and viewed from any remote location—the human is still making the decisions but is now augmented by the robot. If there are harmful hazards workers could be exposed to, it might be a good opportunity to introduce a robot, something that crawls or has a magnetized track (think of working at heights). With exoskeletons, the question is “Where’s the less hazardous work being performed consistently or in more repetition?” A welder for example who experiences high shoulder fatigue at the end of his shift might benefit from the use of a shoulder exoskeleton. It just comes down to the hazards and how often the task is performed.
E: Is there any one major problem or obstacle you encountered and successfully worked through?
S: Yeah, and we’re continuing to work through it: Deployment. When you have something that has been evaluated and piloted by hundreds of users, when does that just become the norm? It’s making the transition collectively, looking at it not as emerging technology but as off-the-shelf digital PPE (personal protective equipment). These are things that can save lives today, just as your insulated gloves would. That’s a big leap, but we’re doing it at GE.
These technologies don’t live in labs; they’re ready to go. The obstacle lies in how you communicate that. The effort of taking it to true deployment involves essentially running an internal marketing campaign with commercials and launch kits. You have to build awareness, find stakeholders, understand where the tech should go and who to introduce it to after the pilot. This new product introduction (NPI) is just as, if not more, important than your pilot.
E: I think a few years ago it was how do I create a proof of concept, how do I pilot, and now it’s how do I scale, which is a good sign. So, as far as the different devices you’re testing and using, how do you find these solutions?
S: All sorts of ways: Connecting with folks at events like EWTS or AWE, through industry organizations, with Google alerts, and by benchmarking and sharing tech with other organizations. We’re always on the lookout for new startups, trying to link up with companies coming into the space. Behind that it’s “Okay, as a company what are the top 10 EHS issues we’re trying to solve? Let’s take the data we have and use it as a compass to find the right solutions.”
E: How do you measure or determine the success of incorporating new technologies at GE?
S: What we look for is the ability to quantify that the technology is actually reducing the likelihood of injuries and/or generating more time (reducing the burden of managing risks) and using data to understand the impact. We can reduce 10 ergonomic injuries this year, but what does that mean and what, then, is the ROI of doing a broader investment?
E: Are you looking at AR+VR for EHS or is it still futuristic?
S: Definitely. From a corporate EHS side, we’re looking at it in terms of how to transfer knowledge, how to modernize training packages and content to make it more impactful and increase retention. That’s where true AR and VR make a lot of sense—digitizing training, streamlining the knowledge transfer from systems and records into the work environment, and transferring domain expertise from the more experienced workforce to create content for the junior workforce.
E: Are you using VR to train for dangerous situations that are hard to simulate in real life?
S: Yes, for electrical safety. We’ve got a project going on right now that takes an operator through a complex and highly hazardous electrical safety procedure, showing him the risks in a virtual but realistic way. Digitizing the outcomes of those high hazards and visualizing it to the end user really sticks when workers go out into the real-world environment.
E: Do you think you’ve found your killer application or are you still looking?
S: I don’t know if it’s quite one thing. A system that can do a couple of things would provide immense value. Something like smart eyewear that gives the user access to content during a repair and lets him or her pipe someone in from halfway around the world when encountering a problem. Something that alerts me, as a worker, to unknown energized equipment around me (a voltage sensing band) and also helps determine operationally why one workforce is being exposed to a danger while another doing the same task isn’t. Is it training or malfunctioning equipment?
When you have edge-to-edge systems that can protect the worker directly and push data from the worker and environment back to a system to intervene and do data analytics. Those are killer platforms and there are a few out there that we’re using right now.
E: What is the future of wearable technologies at GE and in EHS in general?
S: In the very near future the technology will mature and we’ll completely digitize the way risks are managed. I think everything is going to have ‘smart’ in front of it. I mean we even have smart safety shoes now, hazard vests, safety glasses, hard hats…Everything is being digitized. Workers will have a digital toolkit of wearables at their disposal as required PPE [personal protective equipment] as well as optional tools they’ll use to augment some of their work. As long as it doesn’t over-innovate the user and has data value, EHS in organizations could potentially get to zero quo (0 injuries and accidents).
E: What would be your advice to EHS managers in smaller organizations just beginning to look at different emerging technologies like wearables?
S: The great thing about coming in new today is there is so much that has already been done for you to leverage. It’s important to start with the problem: What are your critical injury categories at a site, regional and organizational level and then connect the dots to technology solutions. With any new idea, there will probably be someone out there working on it who may have a solution in place, so don’t be afraid to partner externally. In sum, have a plan: work from your problem statement first; leverage what’s been done in the past; and ensure you are able quantify the impact of new technology through existing and new data insights.
The 5th Annual Enterprise Wearable Technology Summit 2018, the leading event for enterprise wearables, will take place October 9-10, 2018 at The Fairmont in Austin, TX. EWTS is where enterprises go to innovate with the latest in wearable tech, including heads-up displays, AR/VR/MR, body- and wrist-worn devices, and even exoskeletons. For details, early confirmed speakers and preliminary agenda, please stay tuned to the conference website.
Image Source: Seeking Alpha