July 26, 2024
Petrobras ASSET VISUALIZATION
In December 2023, it was announced that Halliburton would be developing a digital twin system for Petrobras’ giant pre-salt field offshore Brazil in order to help “reduce expenditure, accelerate production, and improve crude oil recovery rate.”
The digital twin will represent the production system, including the reservoir, wells and subsea network of the site, integrating asset sensors and other information and models like 4D seismic data and smart well completion technology to improve reservoir and equipment performance and ultimately increase oil recovery.
TotalEnergies AUTOMATION
Rockwell Automation was working with TotalEnergies to leverage digital twins as part of a robot fleet management system, or Robotic Supervision System (RSS), for the oil company to drive autonomous operations for offshore platforms. More specifically, digital twins would be used as an interface to operate robots remotely.
TotalEnergies has long been interested in robotics in order to reduce employee exposure to the difficult and hazardous working conditions involved in offshore operations. As a bonus, cutting-edge tech like digital twins and robotics help attract young talent.
SEACOMP VIRTUAL TOURS
Pre-COVID, electronics product manufacturer SEACOMP had an open-door policy for establishing trust with clients, allowing any customer to visit its Dong Guan factory and see its operations first-hand.
When the pandemic hit, SEACOMP sought a new way to show clients what photos and videos could not. Live video chatting wasn’t an option, as many of the company’s customers are located in different time zones. Enter Matterport.
SEACOMP worked with Matterport to create digital twins of its offices and manufacturing facility, enabling virtual walkthroughs of the factory’s equipment and layout. In this way, the company managed to win new business, maintain its high standard of customer service, and save around $250,000 in travel expenses per year.
Digital twins can be applied at every stage of the customer journey and production process for better decision making and quality assurance at SEACOMP. What was originally a sales and marketing tool has become a multipurpose solution for improving communication with client-side engineers, onboarding new employees, analyzing new production lines, and even reconfiguring the factory floor.
SpaceX OPERATIONAL OPTIMIZATION
Elon Musk’s SpaceX uses digital twins to monitor and evaluate systems and optimize operations.
A digital twin of the Dragon capsule, for instance, synthesizes data from hundreds of sensors integrated into the spacecraft, providing a real-time digital replica of the vehicle. The combo of real-time data and simulation enables Mission Control to monitor and adjust trajectories, loads, and propulsion systems with the goal of maximizing reliability and safety during transport.
Toyota ROBOTIC SYSTEM PROGRAMMING
In 2023, the Japanese automaker partnered with Ready Robotics to simulate and program industrial robots for its aluminum hot forging production lines using Nvidia’s Omniverse platform.
Traditionally, programming robotic systems for forging involved working with hot metal parts. Digital twins enable programming in a safe and realistic simulated environment. Once proven in the simulated environment, programs are then seamlessly transferred to live production work cells. In this way, Toyota can program and optimize complex robotic hot forging processes while boosting safety and efficiency.
BONUS: Shahi PRODUCT APPROVAL
The Indian apparel manufacturer creates digital twins of garments to send to brands for approval, speeding up the approval process by around 90%. Previously, a sample would be physically sent to the prospective customer. Digital twins have dramatically improved turnaround time and the customer experience during the sampling process.
Image source: Harvard
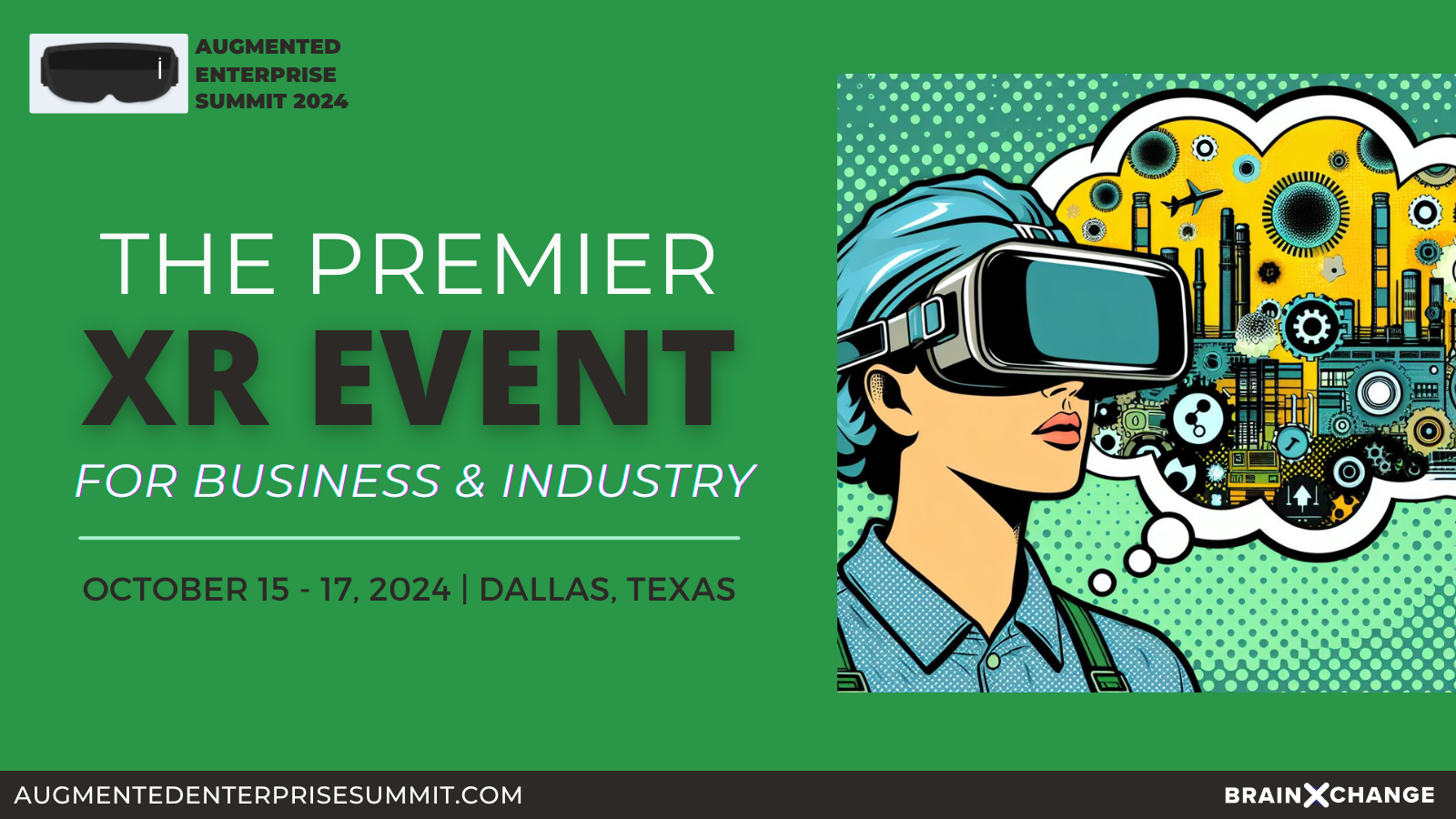